How Microsoft gained 92% visibility with its sentient supply chain system
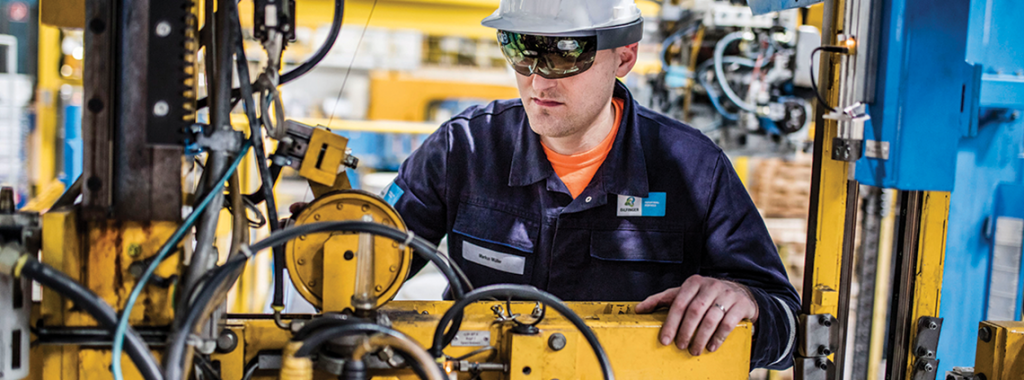
Microsoft is renowned for working at the cutting edge, for its ability to lead on, and influence, major trends in society. And it has a multi-trillion-dollar market value to prove it.
But despite being a corporate heavyweight, it is still a company operating in a volatile space, and as such is prone to the same issues that have battered the supply chains of even the most sturdy organisations. So when materials and shipping challenges emerged, it prompted the company to question its reliance on traditional processes, and to explore how it could apply its passion for problem-solving to the thorny issue of inventory management of its devices supply chain, an area more vulnerable to fluctuations.
A common problem for industry is managing a lack of visibility into tiers alongside instability across all the main touchpoints of demand, including access to and availability of materials and transportation, as well as consumer behaviour. To increase control over these areas, Microsoft decided to move to an order-driven business model.
What is a sentient system?
Microsoft’s vision was to achieve the holy grail – to remove all siloes and turn a melee of discrete tools into what it calls its sentient supply chain – an “all-sensing and monitoring” system that better reflected the nature of the business. In reality, like many companies, it had a fragmented system of information pieced together from across the different business areas.
So step one became: track everything. The team turned to the Internet of Things (IoT) and its ability to create connectivity and autonomous working. Using its own Azure technology, it rolled out a sensor system to track the movements of all items in the process.
The sensors would monitor the movements of items, from the raw materials to the manufacture of finished products, from shipping times and rates, to goods sales, and even returns and maintenance. Azure captured 50 million data points per day, which were fed into a data lake for processing and analysis. Having gone through a rigorous machine learning education, Azure can analyse the vast volumes of data and recognise patterns that indicate potential problems. It could make predictions and optimise itself.
For example, it can predict changes in demand, and from that adjust orders. It can also amend stock movements to ensure different locations have the required inventory levels to lower the risk of excess stock build up or, perhaps worse, stockouts.
But the real jewel is the dual approach of informing decision-making and automating workflows. When analysing data the system can either alert users to meaningful shifts and make predictions, or it can make the decisions for you. For example, before raw materials supplies fall dangerously low, the system may reorder them, or track shipping capacities and times and automatically send instructions to redirect goods to preferred routes.
The power of tech’s reach
Of course, the project was a success. It helped switch from reactive to predictive intelligence, and so far it has saved Microsoft $550m through inventory risk avoidance and delivered 92% data visibility and coverage across the devices supply chain. It is a showcase of what the Internet of Things promised to deliver – a truly connected and intelligent system that helps users not only manage risk but exercise a high level of control while aiming for growth.
Retailer Walmart is also pursuing an intelligent supply chain system to manage its distribution centres. Following a $1.5bn inventory management problem, it plans to create a “next-generation” network to automate storage and retrieval processes across merchandise and food distribution, as well as e-commerce fulfilment centres. Walmart Inc president and CEO Doug McMillon said the increased connections between its supply chain assets will “get us closer to inventory optimisation than ever before”.