BMW’s supply chain makes a quantum leap
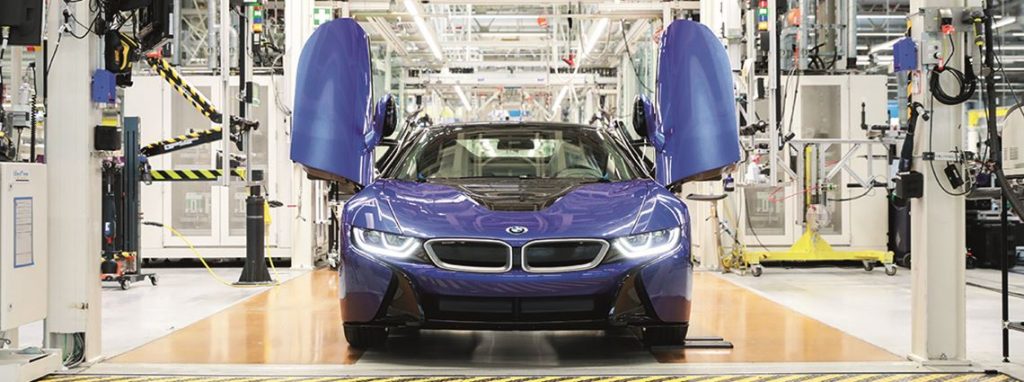
An AI partnership is helping BMW trial methods of streamlining factory requirements
A brand new car looks impressive as it rolls off the production line – almost effortless – but producing a modern vehicle is a complex process. Take BMW’s Mini; the crankshaft alone racks up thousands of miles, starting life in France, transported to a factory in Warwickshire, UK, for finishing, then sent to Germany to be inserted into an engine, before finally being shipped to Oxford, UK, where the engine is fitted into the car.
The company’s 12,000 suppliers in 70 countries means each step in the process needs to be synchronised, as minor delays can cause significant issues. For instance, in 2017, when the supply of steering systems failed, production of four of its models in the UK, South Africa and China was halted, resulting in an estimated sales loss of €400 to €500m per week.
Seeking a technological solution to secure its supply chain, the German carmaker recently teamed up with US-based Honeywell Quantum Solutions and Singaporean start-up Entropica Labs, to trial whether quantum computing could help fine-tune the process.
Why go quantum?
The proof-of-concept project aimed to determine how well a quantum computer could handle the reallocation of assets in the event of a supply chain disruption, and the potential to optimise loads between resources. Specifically, they used an algorithm (the recursive quantum approximate optimisation algorithm, or RQAOA) to tackle a classic problem that deals with task scheduling. This is sometimes known as the ‘travelling Santa problem’, based on the idea that Santa Claus has to calculate the optimum route to take in order to deliver all the Christmas presents in time.
As Honeywell puts it, this optimisation challenge is an “entry point to many logistics and supply chain problems of industrial interest”, and the team pitted a quantum computer against a conventional one to test the results. As expected, the quantum setup achieved better results, which Entropica called “encouraging – and exciting”. The next stage will explore whether a more advanced version of the algorithm could push this even further.
Quantum computers are far more powerful than conventional ones, therefore, they should be ideal for working out highly complex problems in many fields, including across industrial efficiency. “The expected benefits come from quantum optimisation algorithms, which can be significantly faster than algorithms for conventional computers,” says Ewan Munro, co-founder and CTO of Entropica. “Very generally speaking, discrete optimisation problems are a natural target for quantum computing, including routing, scheduling, planning, etc.,” he adds.
How it works
Supply chains, then, should be ripe for the quantum computing treatment. “Manufacturers like BMW deal with logistics and supply chains that have millions of variables. Quantum computing can process millions of scenarios in parallel compared to the sequential calculations of classical computers. That means supply chain processes and changes can be processed in real-time instead of hours or even days needed by classical machines,” says Paul Smith-Goodson, senior quantum analyst at Moor Insights and Strategy, a consulting and research firm specialising in technology.
The power of these advanced computers derives from the way they use data. Conventional systems use binary bits, or ones and zeros, as their fundamental unit of information, but quantum bits, known as qubits, can have a value of any combination of 00, 01, 10, and 11. “A quantum computer’s qubit can represent three values instead of two. Each time another qubit is added, it doubles the power,” explains Smith-Goodson. In short, they can process far more data and more complex information at a faster rate.
How is this actually done? This is where it all gets a bit sci-fi. Rather than using the familiar circuits and chips made of silicon which you would find in your laptop or phone, quantum computers use particles to store information. The Honeywell machine used in the BMW tests uses what’s called “trapped-ion-based quantum computing hardware”. Charged particles are suspended by electromagnetic fields and qubits are stored in stable electronic states of each ion, and quantum information can be transferred through the collective motion of the ions.
Will supply chains go quantum?
If this is all a bit mind-blowing, don’t worry: businesses won’t be using this technology on a large scale yet. “Currently, no quantum systems are being used in a production or operations role,” says Smith-Goodson. “When quantum computing can be integrated into operations, it will be in a hybrid environment where some work will be performed by classical computers and some by quantum systems.”
Entropica’s Munro also advises that although these computers will be able to make calculations quickly, “not every problem will be amenable to these speedups, and moreover, the problem will likely need to be quite large for there to be a benefit to using quantum approaches”. He adds that “in this sense, quantum computing will not impact all problems related to supply chains – the conditions will need to be right.”
When will we see quantum computers getting to work on real-world business problems? Optimists believe they could be playing a role in businesses within five years, while others suggest this will be closer to 10 years. According to Munro, certain areas that are more “naturally quantum-mechanical” will be affected first, such as physics or chemistry applications, before the technology inevitably filters directly down to supply chain management. So while BMW is certainly blazing a trail and is significantly further ahead than most companies right now, forward-looking supply chain professionals should keep a keen eye on the journey, as there may be opportunities to join the race.